کاربرد آهک در صنعت فولاد
فولاد سازی از گذشته تا به امروز
به نقل از رسول دانیال زاده نمین، فولاد سازی را بخشی از صنعت فلزات که به استخراج و فرآوری آهن اختصاص داده شده است، تعریف می کنند. واقعیت این است که آهن، پس از اکسیژن، سیلیکون و آلومینیوم، یکی از عناصر فراوان روی زمین است.اولین آهن مورد استفاده احتمالاً آلیاژی از آهن (Fe) و نیکل (Ni) بود که وقتی گرم می شد، احتمالاً به طور تصادفی، می توانست خم شود و بنابراین برای ساخت تیر و ابزار مورد استفاده قرار گیرد.
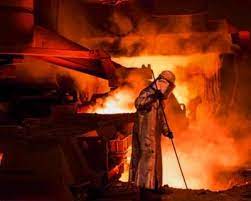
در قرن دوم بود که اولین کوره های تصفیه مواد معدنی حاوی آهن ساخته شد، اما تاسیسات اولیه بودند و دمای کافی برای ذوب فلز تولید نمی کردند. پس از قرن هفدهم از نظر ارتفاع کوره ها افزایش یافته و روش های دمیدن هوا نیز بهبود یافت، این بدان معنا بود که ذوب قالب امکان پذیر بود و بنابراین اولین آهن ریخته گری ظاهر شد. و سپس در سال ۱۷۵۰ اولین فولاد همگن پس از گرم شدن آهن و ذغال در دیگ ذوب به دست آمد.
اگرچه استفاده از آهن به پیش از تاریخ برمی گردد، اما پیشرفت هایی در زمینه ساخت فولاد تا قرن نوزدهم با توسعه راه آهن صورت نگرفت. این زمانی است که نیاز به داشتن ماده ای سازگار برای اولین بار ظاهر شد.در این لحظه از زمان، به دلیل عمده کارایی و تنوع محصولات قابل تولید از آن، تولید فولاد در جهان ۲۰ برابر بیشتر از سایر فلزات است.
طبقه بندی محصولات فولادی
آهن، انواع فولاد، آلیاژهای فرو، سنگدانه های آهنی و آلیاژهای مخصوص آهن. در این میان فولاد به خصوص قابل توجه است، ماده ای کاملاً متنوع که ۸۰٪ تولید فلز را تشکیل می دهد و از اختلاط آهن (Fe) و کربن (C) بدست می آید. محتوای کربن در فولاد از ۱٫۵٪ فراتر نمی رود، در حالی که آهن ریخته گری که از آلیاژهای Fe-C نیز هست، محتوای کربن بیشتری دارد (بین ۲ تا ۴٫۵٪)، که سختی آن را افزایش می دهد.سنگ آهک در صنعت فولاد یا پودرکربنات کلسیم به عنوان عنصری ضروری برای تصفیه محصولات فلزی است
فرآیند ساخت فلز را نمی توان بدون استفاده از پودرکربنات کلسیم تصور کرد که مأموریت آن خالص سازی محصولات به دست آمده در آسیاب فولاد با اصلاح ترکیب آنها است. به طور خاص، اکسید کلسیم یا آهک زنده می تواند این سه عملکرد را در صنعت فلزات اجرا کند:
- تشکیل سرباره: از اکسید کلسیم در تشکیل سرباره استفاده می شود که علاوه بر این، مواد زائد حاصل از تولید فولاد را تجمیع می دهد. علاوه بر این، این فلز را از عناصر موجود در اتمسفر مانند نیتروژن و هیدروژن محافظت می کند، همچنین عایقی است که اجازه می دهد دمای بالای فرآیند (۱۶۰۰-۱۸۰۰ درجه سانتیگراد) حفظ شود.
- حذف فسفر: فسفر موجود در سنگ آهن و ضایعات فلزی که برای شروع فرآیند ساخت فولاد استفاده می شود، می تواند به خصوصیات فولاد آسیب جدی برساند. در مقادیر زیاد، شکل پذیری فولاد را کاهش می دهد و باعث شکستگی آن در هنگام کار سرد می شود.
- آهک زنده اضافه شده به فرآیند فلز سازی، فسفر موجود در فولاد را استخراج کرده و نسبت آن را به سطوحی کاهش می دهد که شکل پذیری آن تحت تأثیر قرار نگیرد.
- از بین بردن گوگرد: گوگرد همچنین می تواند با شکننده کردن فولاد، باعث ایجاد ترک شود و به آن آسیب برساند. از این رو از آهک زنده برای کاهش درصد آن در ترکیب فولاد و به حداقل رساندن اثرات منفی آن استفاده می شود.
بنابراین، محققان در حال بررسی یک فرآیند تصفیه هستیم که سنگ آهک در صنعت فولاد یا کربنات کلسیم را اضافه می کند تا یک محصول فلزی با خواص مختلف بدست آورد. فرآیندی که می تواند به دو روش ساخته شود: فولاد سازی اولیه یا فولاد سازی ثانویه.
کاربرد آهک زنده در فولاد سازی و ذوب آهن
آهک زنده به دو صورت معمولی و دولومیتی دارای کاربرد های وسیعی در تولید فولاد به عنوان عامل گدازنده و تصفیه کننده در فراینده های EAF و BOF دارد. آهک زنده عموما نقش حذف کننده فسفر ، گوگرد ، سیلیس و منگنز را در فولاد سازی دارد. آهک همچنین نقش مهمی در تصفیه ثانویه فولاد بازی می کند.
کاربرد آهک در فرایند های مختلف تولید فولاد به شرح زیر است:
کوره قوس الکتریکی EAF : قراضه آهن و استیل مانند DRI ,و HBI و سنگ آهن برای ذوب شدن به کوره قوس الکتریکی منتقل شده و با جریان الکتریسیته ذوب می شود. سپس آهک زنده یا آهک دولومیتی به عنوان عامل گدازنده به کوره اضافه می شود. میزان مصرف آهک زنده به اندازه ۵۰ تا ۱۲۰ پوند به ازای هر تن فولاد است. در صورت استفاده از آهک دولومیتی باید ۵۰ درصد بر مقدار آن افزوده شود. آهک زنده یا آهک دولومیتی قادر به حذف ناخالصی ها از طریق ایجاد سرباره ای که بر روی آهن مذاب تشکیل می شود است.
در صورت عدم استفاده از ابزار های تزریق آهک زنده میکرونیزه می توان از آهک زنده کلوخه برای این منظور استفاده کرد. برخی از کارخانجات ذوب آن به جای استفاده از آهک زنده یا اکسید کلسیم از مگنزیا یا اکسید منیزیم استفاده می کنند. این ماده با اینکه ازآهک گران تر است اما طبق اعلام کارخانجات ، سریع تر از آهک زنده ذوب می شود.
کوره اکسیژن پایه BOF : آهن ذوب شده در کوره های ذوب آهن برای تولید فولاد مقاوم در برابر حرارت باید به کوره پایه اکسیژنی منتقل شود. سپس اکسیژن با سرعت بالایی به آهن مذاب تزریق می گردد ، در نتیجه کربن و ناخالصی ها اکسیده می شوند. آهک زنده در مراحل مختلفی در این روش کاربرد دارد. برخی کارخانجات ، فلز داغ را در ماشین آلات دیگری سولفور زدایی می کنند. آهک زنده برای حذف فسفر و گوگرد از فولاد کاربرد دارد. آهک زنده عموما بعد از شروع دمیدن اکسیژن به داخل کوره افزوده می شود تا ناخالصی های سولفور و سیلیکا به صورت سرباره از فلز مذاب حذف شود. میزان مصرف آهک در این فرایند ، ۱۵۰ پوند به ازای هر تن فولاد است.
آهک زنده (اکسید کلسیم) را برای سه کار اصلی مورداستفاده قرار میدهند:
- ایجاد سرباره: آهک برای ایجاد سرباره (که ناخالصیهای سنگآهن را دارد) به کار میرود. بهعلاوه آهک همچون یک عایق کمک میکند تا فلز در برابر عناصری مثل نیتروژن و هیدروژن محافظت شود.
- حذف فسفر: فسفر در سنگآهن باعث سایش آن میشود. در حجم بالا علاوه بر سایش باعث میشود تا شکلپذیری فولاد کم شده و پس از سرد شدن باعث شکستن آن میشود؛ بنابراین قبل از شکلدهی فولاد، با افزودن آهک، فسفر را از آن خارج میکنند.
- حذف گوگرد: وجود گوگرد رد ترکیب فولاد باعث شکنندگی و ترد شدن آن میشود. این خصوصیت در زمان شکلدهی موجب ترک خوردن آن میشود؛ بنابراین باید گوگرد را از آن حذف کنند تا تأثیر منفی را از بین ببرند.
کاربرد آهک در صنعت فولاد
· کوره قوس الکتریکی:
در این کورهها موادی مثل قراضه آهن و فولاد، آهن خام و سنگآهن با حرارتی که در اثر جریان برق تولید میشود، ذوب میشود. به کوره قوس الکتریکی آهک اضافه میکنند تا علاوه بر حذف ناخالصیها و شکلدهی سرباره، بهعنوان گدازه آور نیز عمل کند.
· کوره اکسیژن پایه:
سپس آهن مذاب را به کوره اکسیژن پایه وارد میکنند. اینجا با سرعت بالا به درون آهن مذاب اکسیژن تزریق میشود. این عمل باعث میشود تا کربن و ناخالصیهای آن اکسید شوند. افزودن آهک در مراحل مختلفی از این کوره انجام میشود. در برخی از کارخانهها حذف گوگرد را خارج از کوره انجام میدهند (از آهک پودری استفاده میشود).
· فولادسازی ثانویه:
بااینکه فرایندهای زیادی در کورههای قوس الکتریکی و اکسیژن پایه بر روی فولاد انجام میشود؛ بازهم برای عرضه به بازار نیاز به فرایند تصفیه دیگری هم هست. در این مرحله تصفیه فولاد برای تولید استیل با خلوص بالا انجام میشود که در آن از آهک برای تنظیم دما یا خصوصیات شیمیایی فولاد و خارج کردن ناخالصیهای باقیمانده استفاده میشود. در این مرحله فولاد با اضافه شدن آهک و مواد دیگری مثل آلومینا گوگردزدایی شده و از جذب مجدد آلودگیها جلوگیری میشود.
جدول دانه بندی و بسته بندی آهک و دولومیت که توسط بسیاری از تامین کننده ها قابل ارائه است:
بسته بندی قابل تامین | دانه بندی قابل تامین | نام محصول |
فله، جامبو یک تنی، کیسه ۳۵ کیلویی، کیسه ۳۵ کیلویی داخل جامبو | کلوخه
پودر ۰-۱۰ ۰-۸۰ |
سنگ آهنک کربن دار(کربنات کلسیم) |
فله، جامبو یک تنی، کیسه ۲۵ کیلویی، کیسه ۲۵ کیلویی داخل جامبو | پودر | آهک هیدراته |
فله، جامبو یک تنی، کیسه ۳۵ کیلویی، کیسه ۳۵ کیلویی داخل جامبو | پودر
۰-۶ ۱۰-۳۰ |
آهک کلسینه |
فله، جامبو یک تنی، کیسه ۳۵ کیلویی، کیسه ۳۵ کیلویی داخل جامبو | ۱۵-۲۵
۳۵-۵۰ |
دولومیت |
فله، جامبو یک تنی، کیسه ۳۵ کیلویی، کیسه ۳۵ کیلویی داخل جامبو | پودر
۰-۶ ۱۰-۳۰ |
دولومیت کلسینه |
کاربرد آهک هیدراته در صنعت فولاد
آهک هیدراته نوع دیگری از آهک است که بهصورت خشک یا محلول مورداستفاده قرار میگیرد. اغلب برای تولید کابل، برای پوشش دهی در حالت آهن خام یا سرباره بهعنوان سفید کار، بهعنوان روان کننده، برای جلوگیری از چسبیدن مواد به هم کاربرد دارد. آهک هیدراته را برای محافظت از محصولات فولادی در برابر خوردگی فولاد در برابر با اسیدها؛ استفاده میکنند. همچنین از آهک برای خنثی کردن ضایعات اسیدی تهنشین شده استفاده میشود. برای پاک کردن اسیدهای چسبیده به فولاد، آن را از داخل محلول آب و آهک عبور میدهند.